Digitalisation is constantly driving the development of new products, services and business models. In this context, it is often said that the use of big data, Artificial Intelligence (AI) or the Internet of Things (IoT) could also save costs in battery production and make the manufacturing process more sustainable. But is that really the case? Researchers have now investigated this in more detail.
Battery production requires a lot of energy and raw materials
The production of batteries for electric cars or for the temporary storage of green electricity requires a lot of energy and raw materials. At the same time, more and more gigafactories for battery cells are being built in Europe. 40 such gigafactories require around ten gigawatts of power plant capacity to cover their energy requirements. In addition, many rare and critical raw materials such as lithium, nickel, manganese, cobalt and graphite are used in the batteries. The production of battery cells also generates a high level of waste, which has to be recycled. In order to increase efficiency in the utilisation of raw materials and the energy input, the Fraunhofer FFB and Accenture therefore recommend digitalising the production lines for battery cells in their study “The Power of Digitalization in Battery Cell Manufacturing.”
Survey among battery experts provides key insights on digitalisation
For the research, Fraunhofer FBB and Accenture surveyed 143 battery and digitization experts primarily from companies in Europe and North America in two stages. In the first step, the experts identified particularly effective use cases for digital solutions in battery production. In the second step, these cases were integrated into the model of a battery factory with a capacity of 40 gigawatt hours, based on which the experts assessed and calculated the potential savings for each use case and production stage.
The main result: Digitalisation makes the production of batteries cheaper and cleaner. Other key findings of the study:
- Electrode production takes centre stage in digitalization efforts.
- Digital technologies drive down costs in battery cell manufacturing.
- Tracking and optimization drive sustainability gain.
- Virtual commissioning and traceability save $30M annually in cell manufacturing.
- A strategic approach can lead to the most value.
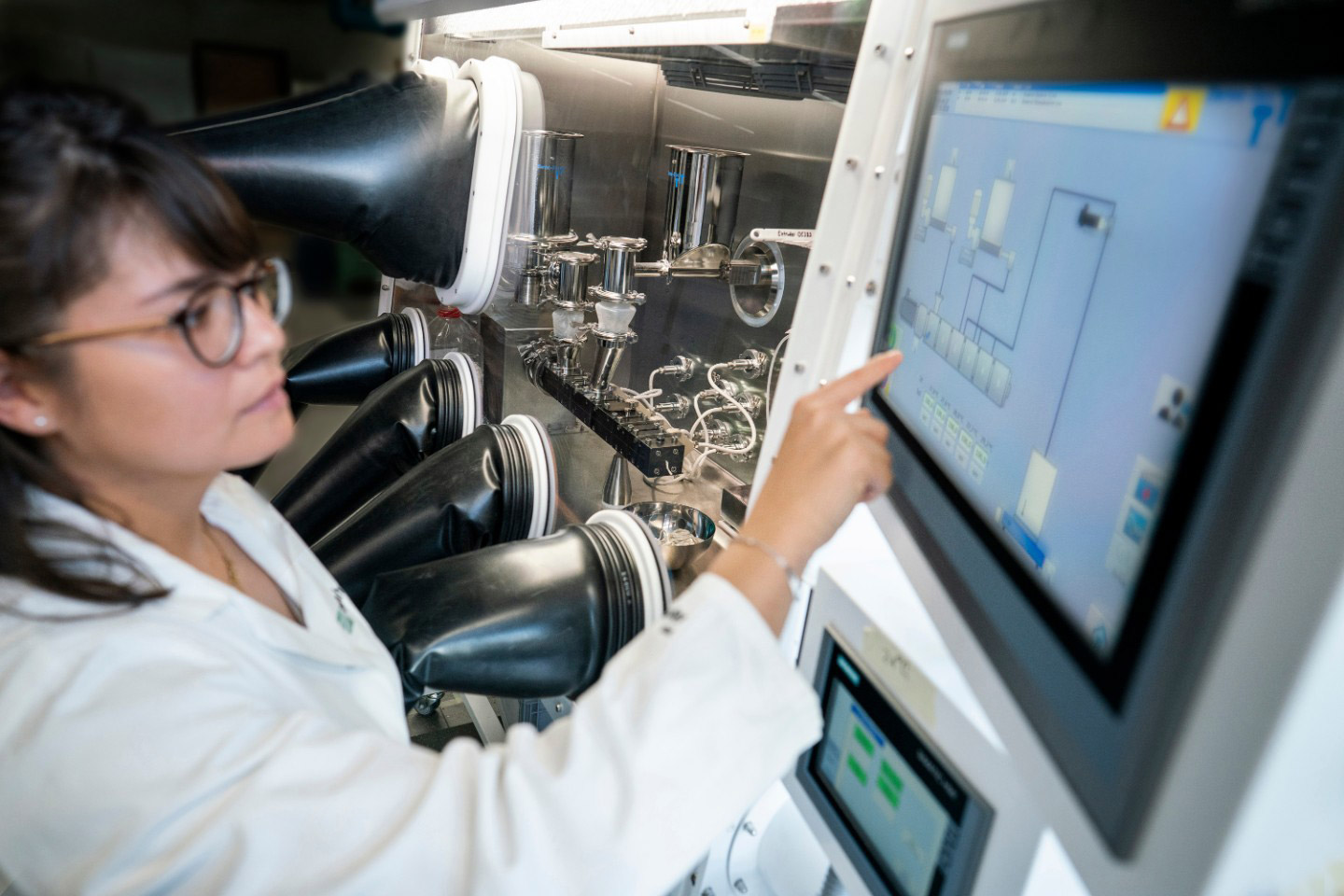
Digitalisation makes the production of batteries cheaper and cleaner
According to the study, a cell factory for lithium-ion batteries with a capacity of 40 gigawatt hours could save up to 27 million euros per year and almost 10 per cent of its emissions with the help of digital solutions. Furthermore, digitalisation could also reduce the reject rate. High reject rates are a known problem in the mass production of battery cells. They can be reduced by up to 10.3 per cent compared to conventional production with digital quality and traceability solutions, for example. At around 70 per cent, material costs account for the largest share of the total manufacturing costs of a battery cell. Digital solutions could make a particular contribution to reducing costs and avoiding waste.
According to the researchers, energy consumption currently accounts for around 5 per cent of production costs. Digital tracking and optimisation technology offers potential savings of up to 9.5 per cent here. Lower energy consumption is also the main driver of potential emission savings of up to 9.7 per cent. Downtimes of production machines, another cost factor, can be reduced by up to 7.1 per cent with digital applications for predictive maintenance, for example.
Summary of the study
In summary, digital technologies offer a way to produce battery cells more cost-effectively while enhancing resource efficiency. The results highlight the critical need for agreement on key performance indicators (KPIs) for battery production and plant performance metrics. They also provide a techno-economic framework for evaluating the complex dynamics of investments in digital manufacturing solutions. The implications for both industry and research are significant, encouraging stakeholders to strategically prioritize use cases based on calculated business impacts. As the global battery cell manufacturing sector scales to terawatt-hour levels this decade, even minor improvements in resource efficiency and sustainability will have a considerable effect. The study’s insights demonstrate that such advancements are achievable through digitalization.
The full report “The Power of Digitalization in Battery Cell Manufacturing” can be downloaded for free here: Digitization in Battery Cell Manufacturing
The learning module “Battery Data” of the EBBC online battery training provides background information on why digitalization is important in the battery industry and the necessity and importance of a digital mindset. More information: https://www.batterybusinessclub.com/explore/battery-data/