What to learn about lithium batteries in this blog?
Lithium-ion batteries have become an essential part of our daily lives, powering devices, vehicles, and renewable energy systems. Their importance lies not just in their performance but also in their potential to shape a sustainable energy future. This blog gives an overview of their core materials, step-by-step manufacturing process, environmental considerations, and cutting-edge innovations in battery technology.
Understanding lithium battery materials
Core materials and their roles.
Lithium-ion batteries rely on four essential components that work together to deliver energy efficiently and reliably:
1. Anode (negative electrode):
- Typically made from graphite, the anode stores lithium ions during charging and releases them during discharging. Graphite’s layered structure allows for reversible lithium-ion storage.
- Emerging alternatives like silicon offer significantly higher capacity but require innovations to handle expansion during charge cycles.
2. Cathode (positive electrode):
- A critical component dictating energy density and voltage. Common materials include lithium cobalt oxide (LCO), nickel manganese cobalt (NMC), and lithium iron phosphate (LFP).
- High-nickel cathodes are being developed for greater energy density, while LFP excels in safety and longevity.
3. Electrolyte:
- Acts as the medium for ion transport between the anode and cathode. It is composed of organic carbonate solvents, lithium salts (e.g., LiPF6), and additives to improve performance and reduce degradation.
4. Separator:
- A thin microporous membrane prevents direct contact between electrodes while allowing ions to pass through. This critical safety feature ensures reliable operation.
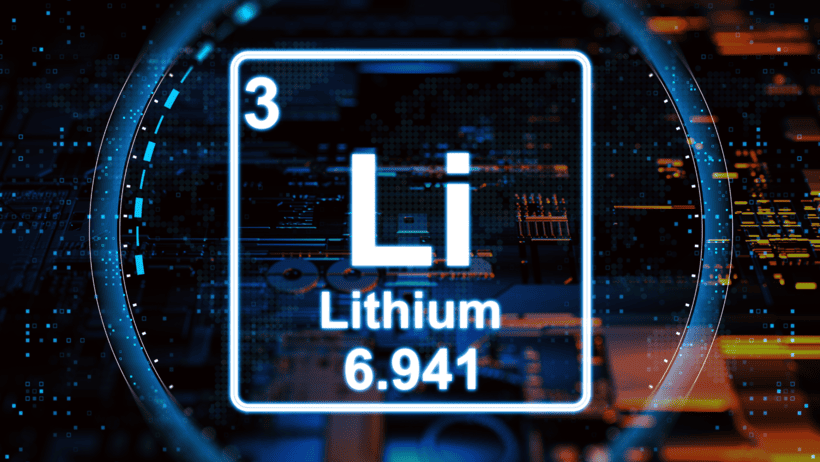
Key takeaways:
- The anode and cathode are the energy-storing workhorses of the battery, while the electrolyte and separator ensure smooth and safe energy transfer.
- Future advancements in materials like silicon anodes and high-nickel cathodes aim to increase capacity and energy density while reducing reliance on scarce materials.
Lithium battery cell manufacturing: step-by-step process
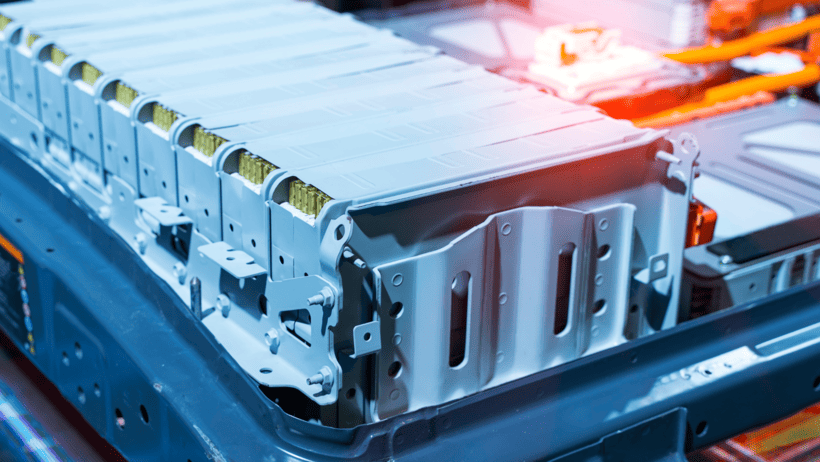
1. Materials handling
The foundation of battery manufacturing is proper handling and preparation of raw materials, particularly powders used in electrodes:
- Powders are characterized for properties such as particle size, shape, and purity, ensuring consistent performance across the production process.
- Cleanroom environments or inert atmospheres minimize contamination and prevent oxidation during handling.
2. Paste production
The next step involves creating slurries or pastes for the electrodes:
- Key ingredients: Active materials (e.g., lithium compounds), conductive additives, binders, and solvents.
- Proper mixing ensures uniformity, which is critical for consistent performance during charging and discharging.
3. Coating processes
The electrode paste is evenly coated onto metal foils (current collectors) such as aluminum (cathode) or copper (anode):
- Techniques: Slot-die and roll-to-roll coating are standard for precision and efficiency.
- Drying: Removes the solvent, leaving a solid layer. This step is energy-intensive, driving the need for optimized drying methods.
4. Electrode cutting and assembly
The coated electrodes are cut into specific shapes and stacked or rolled to form battery cells:
- Precision: Ensures uniform layer dimensions, which is critical for consistent performance.
- Configurations: Cylindrical (e.g., Tesla), pouch, or prismatic shapes are used based on the application.
5. Electrolyte filling
Electrolytes, tailored to the cell’s chemistry, are injected under vacuum:
- This process ensures complete wetting of the electrodes, preventing dry spots that can reduce performance.
6. Formation and aging
The cells undergo controlled charge-discharge cycles to stabilize the solid electrolyte interphase (SEI) layer:
- The formation part of the cell finishing process involves charging and discharging the battery slowly to build up the solid electrolyte interphase (SEI) layer. This layer, which forms on the electrodes, is crucial to battery performance. Batteries with an improperly formed SEI can experience short lifespans and reduced capacity.
Key takeaways:
- Battery cell manufacturing involves highly controlled steps, from materials preparation to formation cycling, ensuring consistency and safety.
- Advances like automated assembly and optimized drying techniques are critical for cost and energy efficiency.
Sustainability in Lithium battery production
Energy-intensive processes
Certain steps, such as electrode drying and electrolyte formation, are energy-demanding:
- Heat recovery systems and dry electrode technologies are emerging solutions to reduce energy consumption.
Recycling and second-life applications
Recycling addresses two key issues: raw material scarcity and waste:
- Advanced methods recover valuable materials like lithium, cobalt, and nickel.
- Second-life applications repurpose used batteries for energy storage systems, extending their usefulness.
Green innovations
Efforts to improve the environmental footprint include:
- Aqueous processing: Replacing organic solvents with water-based alternatives.
- Solid-state batteries: Eliminate flammable liquid electrolytes and simplify recycling.
Key takeaways:
- Recycling and green manufacturing techniques are essential for reducing the environmental impact of battery production.
- Second-life applications and solid-state batteries are promising paths toward sustainability.
Next-generation batteries
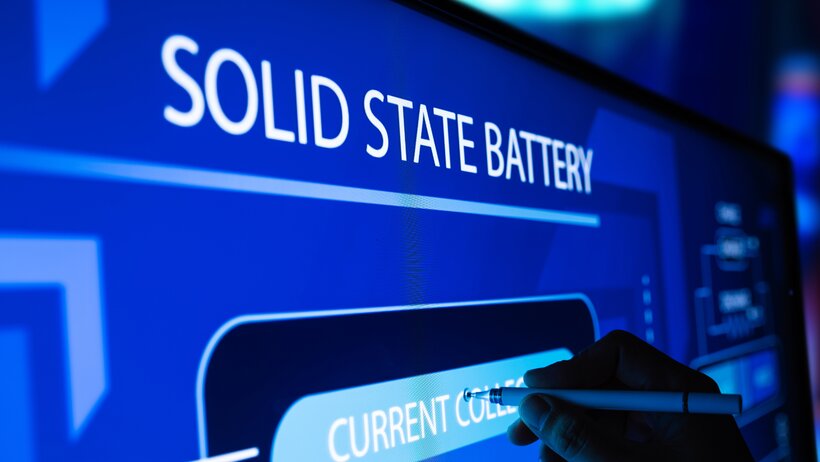
Solid-state batteries
These batteries replace liquid electrolytes with solid materials, offering:
- Higher safety: No risk of leaks or thermal runaway.
- Greater energy density: Improved packaging efficiency.
Lithium-sulfur batteries
By using sulfur in the cathode, these batteries promise:
- Lower cost due to sulfur’s abundance.
- Challenges remain in mitigating the polysulfide shuttle effect, which reduces cycling efficiency.
Metal-air batteries
These innovative systems utilize oxygen from the air as a reactant:
- Unparalleled energy densities make them ideal for grid storage.
- Their primary challenge is electrode stability during repeated cycles.
Digital integration
AI and digital twins are transforming manufacturing:
- Real-time monitoring detects defects early, ensuring quality.
- Process optimization reduces waste and improves efficiency.
Key takeaways:
- Future battery technologies like solid-state, lithium-sulfur, and metal-air hold the potential to significantly enhance safety, performance, and sustainability.
- Digital tools like AI are revolutionizing the production process, ensuring higher precision and lower costs.
Summary of this blog about Lithium material
Lithium-ion batteries have revolutionized energy storage, driving innovation across multiple industries. Understanding their materials, manufacturing processes, and sustainability challenges highlights their transformative potential. With advancements in solid-state technology, green production, and AI-driven manufacturing, the future of lithium batteries is set to be safer, more efficient, and environmentally friendly.
Ready to dive deeper with our experts in our Online Battery Training Program? Click here to learn more!
FAQs on lithium batteries and their manufacturing
Why are lithium-ion batteries so widely used?
Their high energy density, lightweight construction, and long lifespan make them ideal for applications ranging from consumer electronics to electric vehicles.
How does solid-state technology improve battery safety?
By replacing flammable liquid electrolytes with solid ones, the risk of thermal runaway is virtually eliminated.
What are the environmental challenges of lithium-ion batteries?
Mining of critical materials like lithium and cobalt can have significant environmental impacts. Recycling and sustainable manufacturing processes are key to mitigating these issues.
Why is battery recycling important?
Recycling recovers valuable raw materials, reduces waste, and supports a circular economy for battery production.
What role does AI play in battery manufacturing?
AI helps optimize production by monitoring processes in real time, predicting potential defects, and ensuring consistent quality.
What are the main materials used in lithium-ion batteries?
The key materials are:
- Anode: Typically, graphite, though silicon is emerging as a high-capacity alternative.
- Cathode: Commonly lithium cobalt oxide (LCO), nickel manganese cobalt (NMC), or lithium iron phosphate (LFP).
- Electrolyte: A mixture of organic solvents and lithium salts, tailored for specific chemistries.
- Separator: A porous polymer membrane preventing short circuits.
Why is graphite commonly used as an anode material?
Graphite has a layered structure that allows lithium ions to intercalate (insert) and deintercalate (release) easily, making it highly stable, efficient, and affordable for large-scale production.
What is the role of lithium salts in the electrolyte?
Lithium salts (e.g., LiPF6) facilitate the movement of lithium ions between the anode and cathode during charging and discharging, enabling the battery to store and release energy effectively.
What are the environmental impacts of producing lithium-ion batteries?
The primary concerns are:
- Mining of raw materials like lithium, cobalt, and nickel, which can harm ecosystems.
- High energy consumption during manufacturing, particularly in processes like electrode drying and formation.
- Use of toxic solvents in traditional electrolyte production.
How are manufacturers addressing the environmental challenges of battery production?
Solutions include:
- Recycling: Recovering critical materials from used batteries.
- Aqueous processing: Replacing harmful solvents with water-based alternatives.
- Solid-state batteries: Reducing the need for liquid electrolytes and simplifying recycling.
What is a solid electrolyte interphase (SEI), and why is it important?
The SEI is a thin, protective layer that forms on the anode during the first charge cycle. It prevents unwanted side reactions between the electrolyte and the anode, improving battery life and stability.
What is the difference between cylindrical, pouch, and prismatic cells?
- Cylindrical cells: Rolled like a jellyroll, robust and commonly used in EVs (e.g., Tesla).
- Pouch cells: Lightweight, flexible, and ideal for smartphones and tablets.
- Prismatic cells: Compact and sturdy, often used in high-performance electric vehicles.
Why is cobalt being phased out in lithium-ion batteries?
Cobalt is expensive, scarce, and associated with unethical mining practices. Manufacturers are developing cobalt-free chemistries like lithium iron manganese phosphate (LFMP) to address these issues.
What makes lithium iron phosphate (LFP) batteries safer than other types?
LFP batteries have excellent thermal and chemical stability, making them less prone to overheating or catching fire, even under extreme conditions.
How do lithium-sulfur batteries differ from lithium-ion batteries?
Lithium-sulfur batteries replace cobalt and nickel with sulfur, a more abundant and less expensive battery material. They offer higher theoretical energy densities but face challenges with cycling stability due to polysulfide shuttling.
What are the key factors affecting battery life?
- Material quality: Impurities or defects in anode, cathode, or electrolyte materials.
- Charge-discharge cycles: Frequent deep discharges shorten lifespan.
- Operating temperature: High temperatures accelerate degradation.
- SEI stability: A poorly formed SEI layer can lead to faster aging.
How are lithium-ion batteries recycled?
Recycling involves:
- Mechanical shredding: Breaking down used batteries into smaller pieces.
- Hydrometallurgical processing: Using chemicals to extract lithium, cobalt, and nickel.
- Pyrometallurgical processing: High-temperature techniques to recover valuable metals.
What are the benefits of next-generation solid-state batteries?
- Higher safety: Solid electrolytes eliminate risks associated with liquid electrolytes, such as leaks and thermal runaway.
- Greater energy density: Compact designs allow for more energy storage per unit volume.
- Improved longevity: Solid electrolytes are less prone to degradation, extending battery life.
Why is digitalization important in battery manufacturing?
Digital tools like AI and digital twins optimize the production process by:
- Predicting and preventing defects in real time.
- Monitoring equipment to ensure consistent quality.
- Reducing waste and energy consumption during production.
What is the role of binders in electrode manufacturing?
Binders, like polyvinylidene fluoride (PVDF), hold active materials and conductive additives together, ensuring the electrode maintains structural integrity during cycling.
How is cell balancing achieved during manufacturing?
Cell balancing involves matching the capacities of the anode and cathode to prevent:
- Lithium plating at the anode, which reduces battery life.
- Overcharging the cathode, which can cause thermal instability.
What is the future of lithium-ion batteries in terms of sustainability?
Efforts include:
- Developing recyclable materials and improving recovery techniques.
- Reducing reliance on scarce elements like cobalt.
- Exploring alternative chemistries, such as sodium-ion batteries, to diversify resources.
How do aqueous processes benefit battery production?
Aqueous processes replace harmful organic solvents with water-based solutions, reducing toxicity and manufacturing costs while improving environmental safety.
What are the challenges of scaling up next-generation battery technologies?
- Material availability: New chemistries require sourcing or synthesizing materials at scale.
- Manufacturing adaptation: Processes like solid-state battery production require new equipment and techniques.
Can lithium-ion batteries be made entirely from sustainable materials?
Not yet, but ongoing research into alternatives like bio-based binders, solid electrolytes, and abundant elements (e.g., sodium) aims to make this a reality.